Four Runs Microactivity
Four Runs Microactivity -Test Unit MAT ASTM D3907
This unit is a fully automatic and computerized laboratory reactor (described in ES2011993 patent) for analyzing Fluid Cracking Catalysts (FCC). This MAT reactor is designed to perform up to four independent and consecutive FCC tests, following the norms described by the standard method ASTMD 3907, in automatic mode without the presence of an operator.
The operator can adjust for each independent experiment stream time, catalyst/oil relationship, reaction temperature, regeneration times and temperature, gas flow, and other parameters.
With excellent reaction temperature control and using a precise HPLC pump for gasoil dosification, even for a very short reaction time (10 seg), this unit carry out reaction and regeneration in-situ and consecutives stages, with coke and gases analysis. The four liquid products obtained are collected in a cooled receiver until the end of the experiments
CSTR
CSTR
This “Owner Configured” Computerized and automatic pilot plant is based on a CSTR (from 100cc up to 4L and many different alternatives) and the operation is supported by many optional devices as MFC´s, pumps, pre-heaters, separators, pressure control systems,… The customer can design his pilot plant using for it so many options as required for his operation needed, using a configuration sheet.
Technology applied is at the top worldwide. Standarized system becomes short production delivery time and confidence on his performances. The Plant will be High Pressure Certified PED/97/23/EC.
Gases
Until six (n) continuous gases feed lines to reactor. Flow control system by Mass Flow Controllers (Bronkhost High-Tech), including manual valves, check valves, fitting and accessories (P&ID diagram). Gases line preheating system including temperature control loop can be installed.
Liquids
Up to two liquid feed lines can be installed as standard. Pumps can be selected for micro-flow (HPLC from Gilson) or standard process pumps (Dosapro) for different pressures and flows. Relief valves for calibration, check valves, manometers and usual safety devices will be installed. Liquid lines preheating/evaporating systems can be selected. Inertized vessels, tracings and all usual features can be installed.
Stirred Tank Reactor
A stirred tank reactor from Autoclave Engineers, Magnedrive agitator, is the main device of the plant. MOC (SS316, Hastelloy C,…), P@T and volume will be selected by the customer using the configuration sheet.
All safety or operational devices as manometers rupture disk, safety valve and vent valves or sample valves will be included. Also other extra options can be selected. Motor is 3PH but operate with 1PH 220VAC. The temperature control system for reactor, by electrical oven (220 VAC) and alarm cooling system is included. Reaction temperature is measured inside the reactor through a type K thermocouple.
Power control is based on Phase Angle Control (PAC) voltage supply. Over temperature alarm is also included.

Agitation
- Magnetic Drive system “Magnedrive” between the motor and the stirrer.
- Stirrer speeds up to 3300 rpm. Stirring speed sensor.
- Control and display of stirring speed
- The “dispersimax” turbine-type impeller suitable for gas/liquid reactions.
- Cooling Coil. Thermowell.
- Liquid Sample tube with valve.
Heating/Cooling
- Heating with electrical resistance in the vessel of the reactor.
- Optional jacket to heat thermal with fluid.
- Cooling with an internal cooling coil or external baffled jacket.
Wax Collector At High Pressure
Fisher-Tropsch reactions (GTL) can be conducted at this CSTR pilot plant using the waxes SS316 temperature-controlled separator system and an optional switching valve to avoid plugging at the liquid outlet filter. This L/G separator system includes level control based on a differential pressure meter and liquid outlet control valve, also includes heating tracing lines.
Also, a weight scale can be selected on the configuration sheet for real-time acquisition on a computer.
The Two Liquid Phases – Gas Separator At High Pressure
A SS316 liquid1-liquid2-gas patented separator system with no dead volume allows L/G separation even when water and hydrocarbons are obtained simultaneously at the reactor outlet. Level dead volume is nearly 1cc for each liquid phase, which implies real-time liquid outlet, and no accumulation.
The level control system includes a liquid outlet control valve for each liquid outlet. The user can select two models (L/G or L/L/G).
Type of temperature control also can be selected. One or two weight scales for real-time acquisition on the computer can be selected. Pressure control system for the reactor or, when a fractionation is needed, two different pressure controllers for the reactor and separators can be selected. Pressure control is based on the patented PID Eng&Tech microregulation servo-controlled valve (at this brochure). Overpressure interlocks with feeding and oven are installed.
Computer System
Control system based on distributed PID controllers and remote computerized supervision and automation (for process recipes). PC and Process@ software is included. Engineering and Documentation
Multireactor System
High Throughput Multireactor System (8X / 16X)
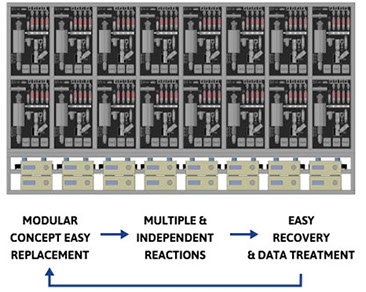
Gasification
Due to the renewed interest in innovative ways to convert the existing fuel reserves with improved technologies like gasification, PID Eng&Tech has worked in collaboration with important researchers in the field of gasification to develop the most versatile pilot plant existing in the market nowadays. Its versatility and complete automatization allow the user to determine optimal experimental conditions and detect possible operational problems in industrial gasifiers.
The most outstanding feature of the plant is its feeding system (pending patent), which has been developed by PID Eng&Tech and can feed up to 1.5 kg/h of different solids and mixtures in a homogenous, constant and reproducible way. The system’s design prevents hot gases from entering the feeding hopper, which would ruin the experiment.
Fluidized Reactor
- The reactor is divided into a reactor zone and a freeboard zone.
- The operating homogeneous temperature is up to 900ºC.
- The reactor zone is Ø = 3” and length = 770 mm. The Freeboard zone is Ø = 5” and length = 535 mm.
- The pressure is measured drop inside the reactor, for fluidization speed determination.
- A particle removal system is installed to collect char and ashes from the bed continuously during the experiments.
- The radiant-type furnace reaches 1000ºC and has two zones to improve the uniform temperature.
Gasifying agent inlets
- Gases streams (air, O2) for fluidizing the bed and gasifying are preheated up to 350ºC – 400 ºC.
- Water is fed utilizing an alternative positive displacement pump and vaporized up to 350ºC – 400 ºC.
- Secondary air is introduced in the middle of the reactor.
Feeding system
The continuous and non-fluctuation feeding system consists of 10 liters hopper and two screw feeders. The solid flow is constant from 0.2 to 1.5 Kg/h.
- A nitrogen flow will continuously flush the dosing screw, promoting the motion of the solids.
Cyclones
Two cyclones connected in series and heated up to 400ºC, allow removing solid particles from gas stream.
Products condenser
A SS316 Shell and multitube heat exchanger is used to cool the hot gases and condense tar and steam.
Filters
Two filter placed in parallel allows to cleaning product gas from smaller particles which are not separated in cyclones.
Control system
- A Programmable Logic Controller controls the alarms of the plant, launching the corresponding actions in case of failure.
- The software is responsible for process monitorization, data acquisition and registration, and experiment automation.
Options
The continuous and non-fluctuation feeding system consists of 10 liters hopper and two screw feeders. The solid flow is constant from 0.2 to 1.5 Kg/h.
- Liquid feeding system (for glycerin).
- Additional hopper for solid feeding system.
Polimerization
Polymerization
The Polymerization Micro-Pilot Plant, developed by PID Eng&Tech, is designed for continuous production at the microscale.
PID Eng&Tech in co-operation with important Research and Technology Centres using different Collaboration Projects has developed a pilot plant to produce polyolefins. The plant comprises two continuous stirred-tank reactors that operate in series.
The plant includes a pre-treating raw material area and a reaction area consisting of two reactor vessels. PID Eng&Tech computerized process control system allows a direct control of temperature, level, pressure and gas composition in the reactors. Micro-Pilot Plant is fully automatized and all of the process parameters, as gas and liquid flows, operating pressure and temperature, residence time per reactor, etc., can be selected by user, or modified in a wide range.
PID Eng&Tech has developed in collaboration with ICP (Catalyst and Petrochemical Institute of CSIC, Spain) systems and devices for solid addition and for catalyst and polymer slurry driving between different reaction steps. These mechanisms have been specifically designed for performing the process at the microscale.
Feed and conditioning of gas and liquid feedstocks
- Gas lines: monomers and comonomers feed streams and nitrogen lines for inertization purposes.
- Solvent lines: Catalyst and cocatalyst feed line.
Reactors and flashes
The plant comprises three SS316 stirred tanks with high pressure closure system. Each one is provided with a magnetically coupled stirred head, a heating jacket, cooling coil, valves and accessories. In addition to temperature, pressure and agitation speed control, composition relations are measure continuously, near-real time.
In this way, the integrated control pressure/relation loop allows the user to work holding simultaneously a stable desired pressure and a stable desired relations during the reaction time.
Distributed control system
All the process variables are controlled by distributed PID controllers. The control system modules are linked with the PC utilizing Process@ software for remote control by digital communications. Remote control will be mean Ethernet way. The system can be controlled manually or automatically, locally or remotely.
All the process and control variables and parameters are registered in only one software application. In addition, the software allows the operator to design automatic procedures for design and automate the run.
Safety system
Plant has several independent safety levels: automatic switch off in case of any problem, pressure, level and temperature security systems; all of that based on a Programmable logic controller (PLC) device independent of the PC. PLC manages the alarm signals from controllers. In addition, actuated valves are configured according to good safety practices.
Supercritical Extraction
Custom Made
Custom Made
Improving competitiveness in the industry is sharply marked by developing new products with high-quality features and a high added value. Continuous and automatic pilot plants that can simulate industrial processes at the laboratory level with reasonable scalability are essential for seeking new products, improving the quality of existing ones, and developing new processes.
These systems’ high degree of complexity, their high number of operating variables, and the interrelationship among them require an exhaustive study of the instrumentation and control to attain results provided by these systems that are representative and reproducible.
An initial commitment toward development, the experience accumulated during 20 years carrying out projects, and strong involvement with customers during the implementation and operation stages accredit PID Eng&Tech as specialists in designing and building pilot plants and laboratory reactors
Simulated Moving Bed Reactor
Serial/Parallel Biodiesel continuos reactor
High-Pressure Co-Gasification with recirculation
Catalytic cracking of Plastics
Reforming and Prox in Microchannel reactor
Slow Pyrolisis Screw reactor
Hydrates Pilot Plant
Atmospheric Pressure Gasification Reactor